Contact Info
E-mail:
Mobile:
Address:
No. 35 Xingye Road, Economic Development Zone, Cangzhou City, Hebei Province



Tee
- Commodity name: Tee
Product Introduction
Specification tee is a type of pipeline connection equipment widely used in fields such as petroleum, chemical, metallurgy, power, and pharmaceuticals. Its main function is to achieve interconnection and fluid transmission between pipelines by connecting three pipes. Below, we will provide a detailed introduction to the length of the three-way connector and its related knowledge.
The length of the three-way connector
The length of a tee usually refers to the length of its main body, which is the part that connects three pipes. The length of the tee may vary depending on different usage scenarios and pipeline specifications. Generally speaking, its length is designed based on factors such as pipeline diameter and fluid pressure to ensure a secure connection and smooth fluid flow.
Characteristics of Three Connections
1. Easy connection: A tee can easily connect three pipes to achieve fluid transmission and exchange.
2. Wide applicability: Three connections are widely used in fields such as petroleum, chemical, metallurgical, power, pharmaceutical, etc., and are suitable for transmission in various media.
3. High pressure bearing: The connecting part of the three-way valve has been specially treated to withstand high pressure, ensuring the safe operation of the pipeline.
4. Diverse materials: The tee can be made of different materials, such as metal, plastic, etc., to meet the needs of different scenarios.
Classification of Three Connections
According to different materials and shapes, tees can be classified into various types. There are three common types:
1. Metal tee: Made of metal, suitable for high-pressure and high-temperature applications.
2. Plastic tee: Made of plastic, lightweight, easy to install, suitable for low-pressure and room temperature applications.
3. Butt welding tee: connected by butt welding, suitable for connecting large-diameter pipelines.
Application area
Three links are widely used in fields such as petroleum, chemical, metallurgy, power, and pharmaceuticals. In oil drilling, the three are commonly used to connect oil pipes and water pipes; In chemical production, the three types of pipelines are commonly used to connect various process flows; In the power industry, the three types are commonly used to connect steam pipelines and water pipelines.
In short, as an important pipeline connection device, the design of the length and other parameters of the tee is aimed at meeting practical application needs. By understanding the length, characteristics, classification, and application fields of tees, it is possible to better select and use tees to ensure the safe operation of pipelines and the smooth transmission of fluids.
Nspection
We pay attention to product inspection and adhere to the principle of "quality first, management first". Each product must be inspected by inspection equipment, such as industrial television testing equipment to check weld seams and appearance quality, magnetic flaw detectors to check steel pipe defects, ultrasonic automatic continuous flaw detectors to detect horizontal and vertical defects in welded steel pipes, X-ray automatic detectors and industrial television imaging equipment to check internal quality, with a sensitivity of not less than 4%. The X-ray film equipment checks the original welds and has a sensitivity of not less than 2%. Hydraulic press and microcomputer automatic recording system are used to test the pressure quality of each steel pipe. Mechanical testing equipment includes hydraulic universal testing machines and computer control systems to test welds, including tensile, guided bending, slotting machines, Charpy impact testing machines, various sample processing machines including lathes, grinding planes, grinders, and chemical composition analysis.
Production Process
(1) Process technology preparation: Select a reasonable steel strip width based on the nominal outer diameter of the steel pipe. Prepare steel pipe welding parameters, steel pipe inspection process cards, and production plans based on raw materials, and distribute them to each production and inspection process.
(2) Uncoiling process: After receiving the production process card, the qualified steel strip is lifted onto the uncoiler according to the production process requirements, and the steel strip is uncoiled and leveled.
(3) After the steel strip is leveled, it runs to the butt welding process, and the butt welding personnel perform the butt welding according to the issued welding parameters.
(4) After the welding of the steel strip is completed, it runs forward to the disc cutting process and cuts the burrs of the steel strip according to the cutting amount specified in the production process card.
(5) After cutting the edges of the steel strip, it runs to the milling process to further process the edges of the steel strip, such as removing burrs and milling off grooves on steel plates larger than 8mm.
(6) After the edge milling treatment of the steel strip, the edge of the steel strip is pre bent to form a "pout" phenomenon in the welding seam during the forming process.
(7) The steel strip enters the forming machine, and the forming worker adjusts the shape according to the issued production process card.
(8) After the steel pipe is formed, the internal welder performs internal weld welding on the steel pipe according to the issued welding parameter table.
(9) After the internal welding of the steel pipe is completed, when the weld seam rotates half a week to pass over the steel pipe, the external welder performs external welding on the weld seam.
(10) In the case of a smaller reduction rate, the steel pipe can achieve a certain required dimensional accuracy and roundness through sizing, and further improve the appearance quality of the steel pipe.
(11) After the external welding of the steel pipe is completed, it continues to move forward. When the top of the steel pipe reaches the specified length requested by the customer, it is transmitted to the plasma cutting machine through a photoelectric sensor for cutting the steel pipe to the specified length.
(12) If there are defects in the steel pipe welds, they can be manually repaired to remove the defects and proceed to the next process.
(13) Process the ends of the steel pipes to make them straight and ensure that the bevel angle meets the standard requirements.
(14) Measure the length and weight of each steel pipe, and control the weight deviation and length within the standard range.
(15) Eliminate the phenomenon of magnetic bias blowing caused by residual magnetism during steel pipe butt welding, and improve the quality of steel pipe butt welding welds.
(16) Spray labels on the inner and outer walls of one end of the steel pipe according to standards and customer requirements.
Key Words
Related Products
The company's business covers more than 60 countries including Germany, France, the United Kingdom, Singapore, Malaysia, Kazakhstan, Uzbekistan, Iran, etc.
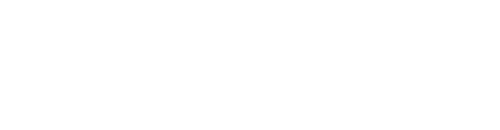
We sincerely invite you to join hands with XCY-PIPE
Create a brilliant future together!
Email us
For more information, please leave your message below.